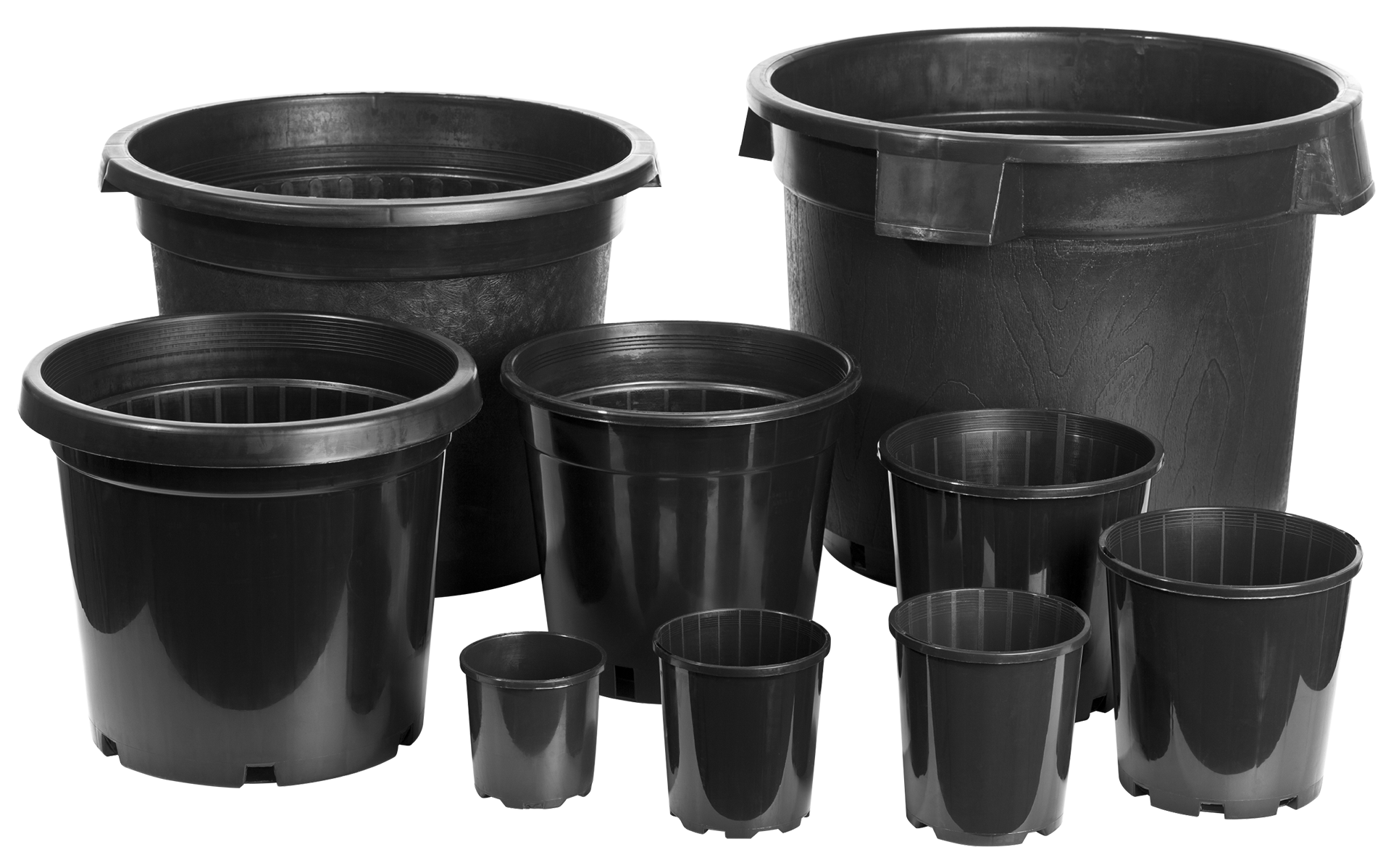
Recycling is a hot topic
Kreuwel Plastics Almelo B.V. has been a producer of high-quality injection molded products since 1979 and has been a loyal customer of Stork IMM for many years. All Kreuwel products are made from 100% recycled raw material. Luc Snijders, third generation of the family within the company, tells us about this subject.
Customer: Kreuwel Plastics
Sector: Pots
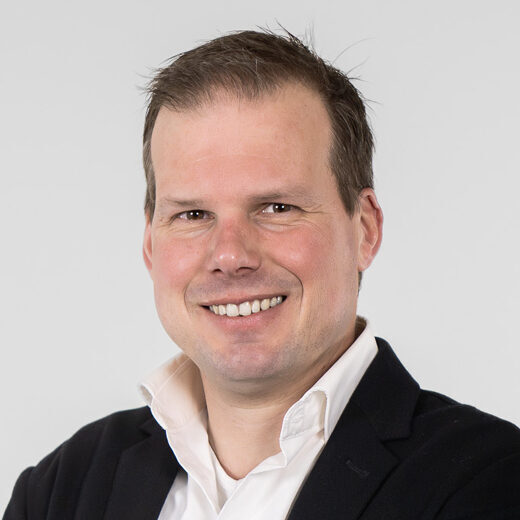
We're happy to help!
Futureproof; automisation of the production process
The world is changing and we will have to change with it. We have to professionalize, Industry 4.0. What has become very topical since several years is the ability to detect the different types of plastics so that they can be separated during waste processing. Infrared sensors are used for this. The classic black flower pot contains a too high carbon black content and therefore has no reflection detection of the infrared light. As a result, the pot is not detected and cannot be separated, with the result that it ends up as landfill or goes into combustion.
Producers of flower pots, among other things, strive to manufacture pots from materials that are “NIR detectable”. All colors within Kreuwel are now 100% recyclable. We can demonstrate this by means of the KIWA Certificate, to which we are subject to regular and strict checks. Every week we carry out a random check with our NIR hand detector and store those products. This allows us to guarantee our customer has a 100% recyclable product, so that they can also guarantee their customers a 100% recyclable product. In comparision to other certifications we test and check the end product and not the raw material from which it is made.
In addition, we distinguish ourselves in the market because all Kreuwel products are made from 100% recycled raw materials. In short, NO prime / new plastics. We are also KIWA certified for this. To ensure this, incoming raw materials are checked both here at the factory and at the manufacturer in order to demonstrate that products are actually made from 100% recycled raw materials. It is important for us as a company not only to say it is true but also to demonstrate it.
Luc Snijders "I think that in the future we will have to extract much more data from our processes on the basis of which we can adjust those processes as much as possible without manual intervention. We have to make work easier for ourselves. Just look at the removal of the products. In the past, some products were still stacked by hand and now they are taken out and stacked with robots. The next step is that we measure more and that we use the data to prevent or correct deviations in the production process, which are now often seen as fact. I think it should be possible for machines to regulate themselves and produce only good products. That is the basis on which you can automate and again, to be able to do more with the same number of people and, above all, to burden employees less physically."
"I expect that our suppliers think along with us as a customer and develop as much as possible. So far that has also been going well with our supplier."
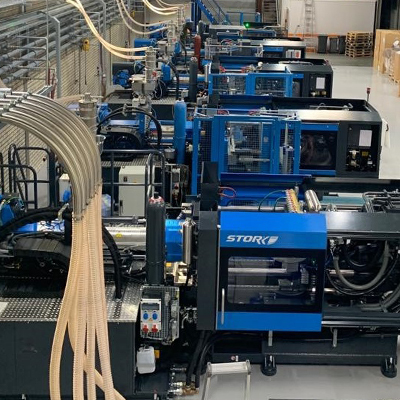
high-performance
Aligned with your production process
Maximum performance, minimal costs, and a sustainable future
Maximum efficiency
Our injection moulding machines are designed for top performance, with maximum uptime and production capacity.
Cost-efficient
Optimize your production process and reduce operational costs with our sustainable and efficient technologies.
Flexible deployment
Our solutions are tailored to your specific production needs, with customizable features for every industry.
Years of experience in machine building
Support and service for maximum productivity
Installed injection moulding machines worldwide
customized solutions
Pot-Line
The Pot-Line from Stork IMM is fully focused on high-performance injection moulding machines for the production of flower pots. The various well-developed options are aimed at achieving maximum uptime, minimal energy use, and extremely short cycle times. Our solutions ensure optimal operational protection and homogeneous melting of recyclate.
We also offer options that contribute to an even more stable production process. Perfect for applications involving recyclate or high-cavity moulds—without compromising on dimensional stability or visual appeal.
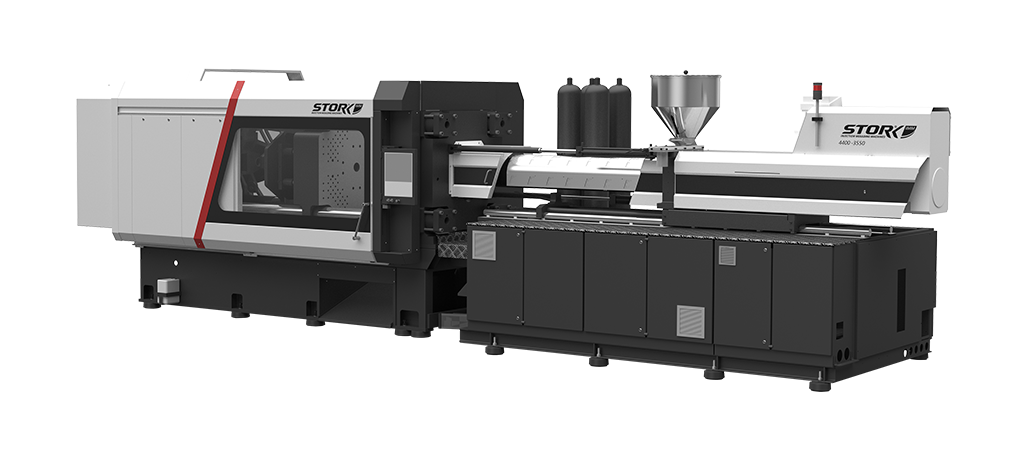