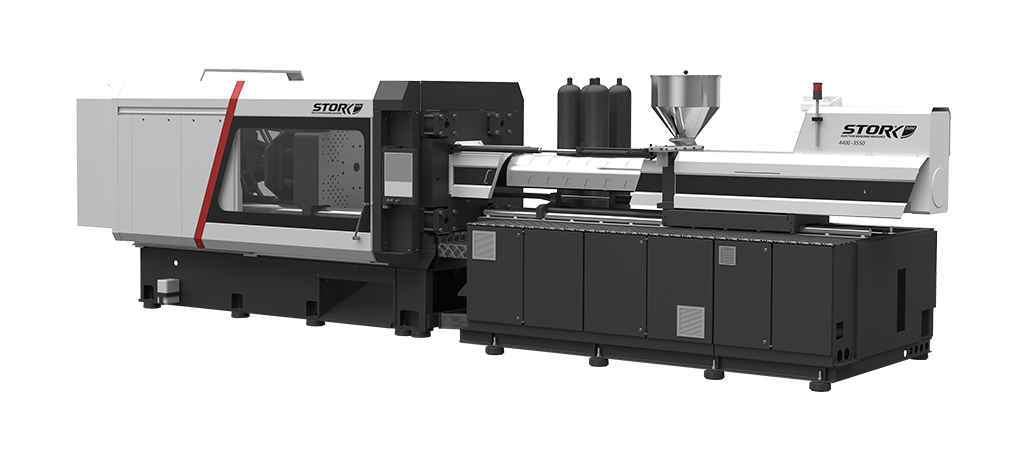
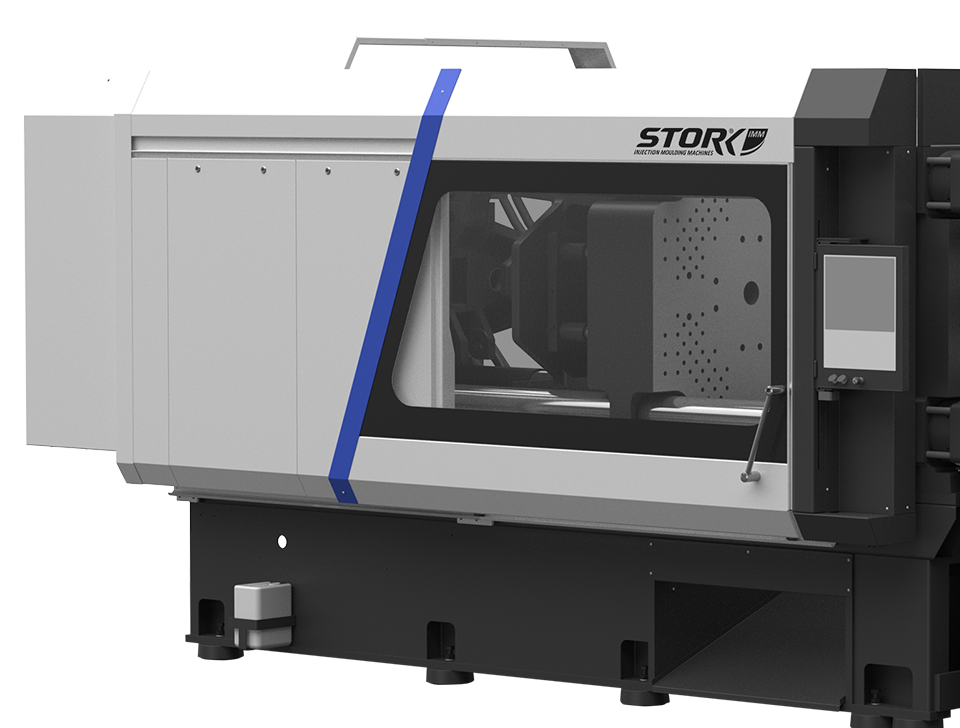
Packed with performance
MachinesYour partner for high-performance injection moulding machines, precisely aligned with your production process.

We're here to help!
high-performance
Aligned with your production process
Maximum performance, minimal costs, and a sustainable future
Maximum efficiency
Our injection moulding machines are designed for top performance, with maximum uptime and production capacity.
Cost-efficient
Optimize your production process and reduce operational costs with our sustainable and efficient technologies.
Flexible deployment
Our solutions are tailored to your specific production needs, with customizable features for every industry.
Years of experience in machine building
Support and service for maximum productivity
Installed injection moulding machines worldwide
circular solutions
Stork IMM Second Life Program
We ensure an extended service life for injection moulding machines. We offer a wide range of premium machines – refurbished, quickly available at attractive prices. In addition, we offer refurbishment for your own machines, enabling significant benefits in energy savings and optimization. We also run various exchange programmes for used parts, ensuring a large stock of refurbished parts – quickly available, at competitive prices.
Premium Used Injection Moulding Machines
A used injection moulding machine; refurbished and up to modern standards. Our premium machines are quickly available at attractive prices. These machines are also available for temporary rental.
support & service
Our Service and Support
At Stork IMM, we are here to assist you at every stage of the process. From initial installation to ongoing support, we offer complete services to ensure your injection moulding machines deliver optimal performance.
news
Stay informed on trends, tips, and news
we look forward to meet you at upcoming
International Tradefairs
Check out our agenda and find out where you can find us. Don't miss the chance to take a look into the world of Stork IMM!
K 2025
8/15 oct 2025
Messe Düsseldorf GmbH (DE)
30. Plastpol 2026
19/22 may 2026
Targi Kielce (PL)
Kunststoffen 2026
September 2026
Brabanthallen 's-Hertogenbosch (NL)